Baritainer® – Barrier Plastics Case Study
The Challenge
Many products require packaging that includes special barriers in order to ensure the integrity of the contents. Barriers that control the migration of aggressive chemicals, container distortion, product loss, and odor emission are available in the marketplace, but most require multiple layers or secondary chemical treatments such as fluorination.
Altium Packaging’s customers needed bottles made with only one layer for smaller annual quantities and without the added costs or limitations of the alternatives.
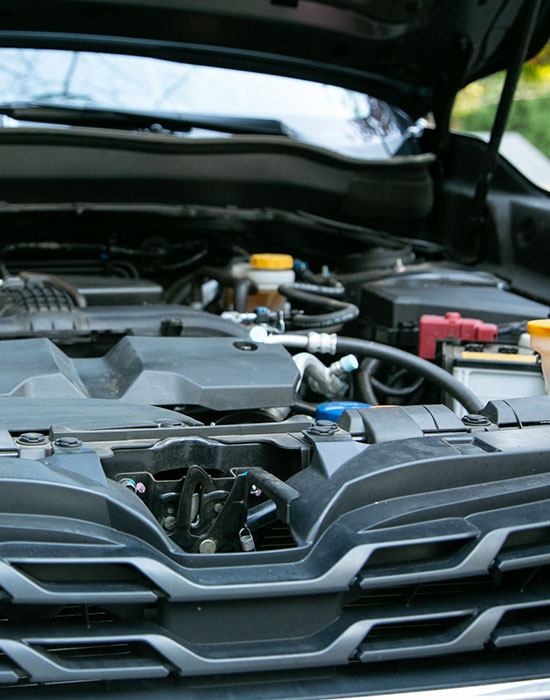
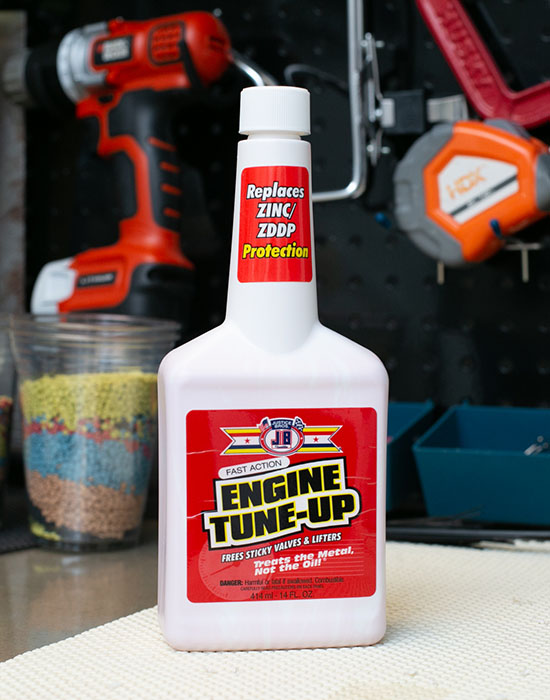
The Solution
Altium Packaging searched for a solution through various organizations and ultimately partnered with Barrier Plastics to utilize their Baritainer® product. Working together, we developed special processing and testing techniques to create a bottle that met Altium Packaging’s high standards and Always Made Right® commitment.
The Results
The result was a monolayer container that is lightweight, recyclable, impact resistant, pliable, and made in just one stage with traditional blow molding equipment.
This innovative product is not only economical but is also safe for a wide range of solvent-based liquids. It even provides flavor and aroma retention and an effective oxygen barrier to support longer shelf-life, which is many times more effective than standard HDPE. Additionally, Baritainer® provides custom barrier protection as the Quoral® additive level can be adjusted to meet a product’s barrier needs.
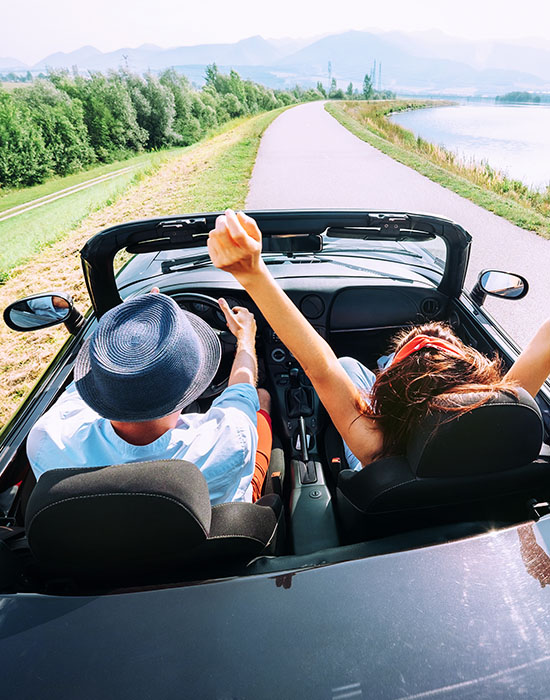